The Four Simple Steps to Safety Excellence
- Get clear, focused, and determined.
Co-create the Safety Strategic Plan© using the Process Enneagram©. Keep it posted, talked about, and used. - Build trust and interdependence.
Develop the shared, co-created Principles and Standards of behavior that are needed to achieve safety excellence. Live by them in doing the work on the Issues that need to be addressed to improve safety performance. Hold each other accountable. Let everyone know you deeply care about safety and everyone going home healthy and in one piece. Make this work open and visible for everyone to see and to model in his or her own work. Trust and interdependence emerge as people learn to work together this way. - Talk with everyone, share information openly, and listen to each other.
Walk around, talking and listening, every day. As people get to know you better and see you being honest and keeping your word, trying to improve yourself and admitting to mistakes when they are made, trust builds.
(Since over 95% of all injuries and incidents are the result of the actions of people, go look at what people are doing. Do Safe Acts Auditing to see and keep track of how people are working. Show the people you really care about improving safety.
These audits give a quick indication of what is happening in the safety culture, providing clues to changes; a drop in the Safe Acts Index (SAI) indicates a potential injury is about to happen. The patterns of behaviors that are seen indicate areas of strength and areas of weakness that need to be addressed. Perhaps there are bad habits or more training is needed, or there is a confusing mixed message or a deeper systems problem needs to be straightened out. When people see and become aware of what is happening, focused attention can be applied.)
- Quickly take the appropriate actions on new information that is created to correct the problems that the patterns of unsafe behaviors observed indicate. Remember that the information developed in these Audits is for learning about how to improve the safety performance. If this Safe Acts Auditing tool is used for punishment, the integrity and value of this process is lost.
Evolve steps 1, 2, 3 and 4 all at the same time as the Safety Leadership Process™ develops. They are all interconnected and interacting all the time. Do them over and over again.- It takes the courage to hold each other accountable, to have the difficult conversations, to make decisions, and to act.
- It requires the care to do every thing as well as you can.
- It requires the concern for the impacts for all the changes on all the stakeholders.
- It requires the commitment to stay the course in both the good and difficult times, day after day, month after month, year after year!
- This is the essence of safety leadership.
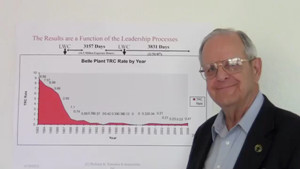